|
QUALITY
Quality Policy :
- We are committed to meeting customer requirements through continual improvement of our
quality management systems.
- We shall produce and supply superior quality products & services and maintain credibility in the
market for the quality of our products & services all the times.
- We are further committed to develop a motivated workforce with a sense of pride in the
organization which will lead us towards being the best in the industry and working in harmony
with the environment.
|
|
Quality :
- To achieve performance excellence through collective efforts and to remain ever dissatisfied as
quality has no finishing line.
- Our Prime focus is satisfy our honorable customers & our prime motto is to meet customer’s
requirements effectively & creating values for all our customers and our company.
- We Pratiksha Brass Industries are committed to manufacture & deliver consistently as per
customer's requirements.
- We Pratiksha Brass Industries are committed to pursue Excellency through continual
improvement in all areas of business processes and to distinguish ourselves by the quality,
delivery & cost efficiency of our products & services with the total Involvement of our
employees.
Training Policy :
Pratiksha group believe in enhancing human resources assets value for continual improvement in
product quality
Periodic training is provided for achieve best quality level to all employee to make things Easier,
faster & cost effective
Periodic measurement of employee’s skills & capabilities are tested with relation to matrix skill & competence skill
In house as well as training from professional bodies are organized. Our competent Quality Assurance team is highly capable of providing an integrated quality
assurance by following strict quality checking at every stage, right from incoming raw material
to final dispatch...
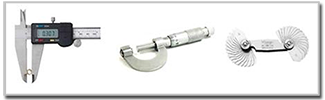
Planning to Achieve Best Quality :
- Test Equipments & Testing Method
- Regular Based Employee Trainings
- In-Process Production Inspections
Calibration & Maintenance of Quality Equipments :
- Up-to-date records of quality standards
- Dedicated Engineering Department
- Design & Development as per Customized Design
- Vendors Controls & Audits for Quality & Delivery Time
- Statistical Measuring techniques like Variance analysis, SPC (CP, CPK, Histogram
Study), X-Chart, R-Chart, trends etc.,
- 100% Visual Inspection to ensure 100% visual defect free products
Quality Assurance:
Owing to the priority to serve quality products, various stringent quality tests are conducted from
the very initial stage of deployment of raw materials in processing unit to the final stage of
launch of end products in the market. For fuller assurance of zero manufacturing defects, quality
control executives personally check the products before final dispatch. |
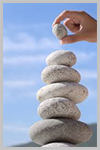 |
|